The era of net-zero homes is upon us. These super-efficient homes use rooftop solar energy production and smaller, electric powered heating systems such as air source heat pumps to produce as much energy as they consume.
That’s some sexy technology, but it only gets us halfway to net-zero. The real secret is insulation.
Peter Amerongen is the principal director at Habitat Studio, a custom home builder and one of the pioneers of net-zero homes in Edmonton, Alberta.
“Insulation is really the backbone of energy efficiency,” says Amerongen. “The more insulation you have in a house, the less energy you're going to use.”
A net-zero home only requires about half the energy it takes to heat a conventional home.
“We're putting in about double [the insulation] that is going into the typical code-built house and about four or five times more than would be in a house from the '50s,” explains Amerongen.
What’s in an R-Value?
Insulation is rated using an R-value, which is a measure of thermal resistance. It is calculated based on two factors:
the thickness of the insulation and how effectively the insulation limits the movement of energy.
The relationship of R-value to insulation value is linear, “If the R-value of your wall doubles, the amount of energy you're losing is cut in half,” says Amerongen. We typically think of R-value as applying to insulation, but we also lose significant heat through our 2x6s, steel beams and concrete in homes. This is called thermal bridging.
“Some materials stop heat flow," says Amerongen. "We call those insulators. And some materials allow heat to flow through them. Steel is a good example of a very conductive material. If you heat up the inside of it, and it's running through the building envelope, it's a pathway, a pipeline for heat out of your building. Concrete is another."
“That 2x6 stud is actually another pathway," says Amerongen. "It's a bit of an insulator, but it's a poor one." You lose heat through the wood at a rate of about five times that of insulation.
Some energy efficient builders now put a layer of foam board insulation outside the wall to cut this thermal bridge off at the knees.
Double studs - creating a true R40 wall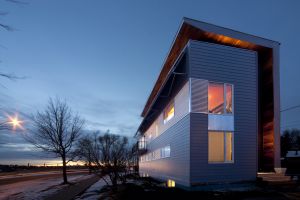
Traditionally, builders use inexpensive R13 batt insulation in 2x4 walls, but due to thermal bridging, this construction gives effectively only R9 of insulation value — hardly enough for a Canadian winter.
Amerongen builds a double wall with added insulation to combat this heat loss.
“We like the double 2x4 wall because it gives us the most economical high R-value,” says Amerongen. “The true energy performance on this is about R40.” That’s more than double the insulation of a standard R20 2x6 wall, where thermal bridging lowers its performance to about R15. “With our double 2x4 wall, we've got a space between our two studs that gets filled with insulation to stop that heat flow.”
That insulation is not batts, but blown-in insulation, which can be chopped up fibre, fibreglass or cellulose.
“We like the cellulose because it's essentially a recycled material," says Amerongen. "It's got the lowest energy content in the insulation itself."
The belfry and basement
Amerongen also blows cellulose insulation into attics to a depth of two feet or more to achieve R80. In the basement, Amerongen shares another secret for energy efficiency.
“The heat loss from a basement wall can be just as high as the heat loss from above ground walls." he says. "We install four inches — two, two-inch layers of expanded polystyrene against the concrete — and then we build a 2x4 frame wall that we put a R22 mineral wool batt in. So we get a total of about R37, R38 in our basement wall."
To kill thermal bridging, Amerongen uses two sheets of hard foam polystyrene insulation under the basement slab to achieve R16, which connects to the foam in the basement wall to form a continuous barrier.
Into the rafters
Spray foam is the most advanced of the commonly used insulators. Once dried, it has the added bonus of acting as its own vapor barrier. Its R-value is also relatively high per inch.
“We use spray foam when we need a high R-value in a relatively thin space,” says Amerongen. This means places like where the rafters meet the walls.
“We also use it to some degree for giving us additional air tightness,” says Amerongen. “Air tightness is a critical part of energy conservation, as important as insulation. A house that's highly insulated but still leaky will find its biggest [energy loss] is air leakage.”
In super energy efficient homes, builders want to reduce air loss to about one air exchange per hour or less. This is how you know you have done a good job with insulation and the envelope of your home.
It is also the reason these efficient homes have advanced heat recovery ventilators that use heat exchange to save heat and provide needed fresh air inside the home.
The final component in the home insulation puzzle are triple glazed windows, some of which achieve R8, a vast improvement over conventional windows.
Peter’s secret formula
And so you have it, one tried and tested formula for the super energy efficient home that requires half the heat of a conventional home.
There are other formulas such as 2x8 walls with spray foam inside and hard foam board on the outside, used by production builder Landmark Homes.
Whatever system you use, the key is energy modeling. “It's like an accounting of where all of the energy of the house is likely to go,” says Amerongen. “Every window, every square foot of wall, every square foot of ceiling, all of those things go into the energy model so you know how much you're losing in each place.”
This crucial step is how you can weigh the cost-effectiveness of one measure over another and get the very best bang for your buck. And it’s this experimentation that has made it entirely practical for custom builders and production builders alike to raise the bar to the point where you can now look after all of your own energy needs right in your own home.